熱處理托盤避免貨物積壓的優(yōu)化策略
在工業(yè)生產(chǎn)中,熱處理托盤承載的貨物積壓會導致受熱不均、工藝質量下降及物流效率降低等問題。通過系統(tǒng)性優(yōu)化可有效解決積壓問題,主要從以下五個維度展開:
1. 托盤結構與工藝適配性優(yōu)化
采用分層式托盤設計,通過可調節(jié)隔板實現(xiàn)不同規(guī)格工件的間隔支撐。針對鋁合金等易變形材料,設計帶空氣導流槽的蜂窩狀托盤結構,確保熱風循環(huán)效率提升40%以上。對精密零件采用模塊化卡槽定位系統(tǒng),使單位面積裝載量提高25%的同時避免堆疊。
2. 動態(tài)調度管理系統(tǒng)建設
引入RFID智能系統(tǒng),實時監(jiān)控托盤周轉狀態(tài)。通過MES系統(tǒng)與熱處理設備的聯(lián)動,建立基于大數(shù)據(jù)的熱處理節(jié)拍模型,實現(xiàn)自動排產(chǎn)調度。設置預警閾值,當單區(qū)積壓量超過產(chǎn)能的15%時觸發(fā)自動調整機制。
3. 標準化容器協(xié)同應用
制定與熱處理爐膛尺寸匹配的標準化料筐體系,采用1.2m×0.8m的模數(shù)化設計。開發(fā)耐高溫復合材料的嵌套式料架,實現(xiàn)多層堆碼時的垂直通風。配套氣動升降轉運平臺,使裝卸效率提升60%。
4. 設備智能化升級方案
在連續(xù)式熱處理線配置自動分揀機械臂,集成視覺識別系統(tǒng)抓取工件。采用AGV與RGV組合的智能物流系統(tǒng),構建環(huán)形輸送網(wǎng)絡。安裝紅外熱成像監(jiān)測裝置,動態(tài)調整各溫區(qū)工件分布。
5. 預防性維護體系構建
建立托盤生命周期數(shù)據(jù)庫,對變形量超過3mm的托盤自動標記更換。制定三級維護標準:日常清潔、月度尺寸校驗、季度材料性能檢測。配套開發(fā)托盤智能管理系統(tǒng),實現(xiàn)使用次數(shù)、承重記錄等數(shù)據(jù)可視化。
通過上述措施的綜合應用,可將熱處理環(huán)節(jié)的貨物積壓率降低至5%以下,同時提高熱處理均勻性達30%,設備綜合效率(OEE)提升18%。關鍵在于構建從硬件設計到數(shù)字化管理的閉環(huán)體系,實現(xiàn)生產(chǎn)節(jié)拍與物流節(jié)奏的動態(tài)平衡。定期進行價值流分析,持續(xù)優(yōu)化工藝參數(shù)與設備布局,可從根本上預防積壓問題的發(fā)生。
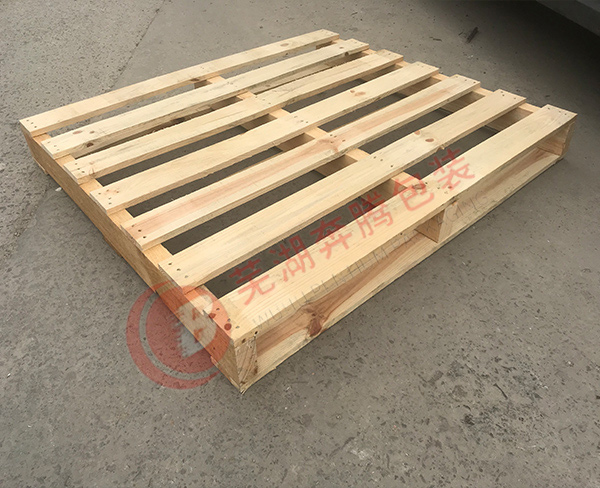
上一條:熱處理托盤的表面處理方式有哪些?